Start devices are used to assist the starting of the compressor. The conditions where start assistance is typically needed are when the compressor is old and worn or the system must start against a higher pressure on the discharge side. Older refrigeration systems used a fixed metering device like an orifice or capillary tube to separate the high pressure side of the system from the low pressure side. The flow rate through the device depended on the difference in pressure. When the system shut off the pressure would equalize somewhat rapidly through the fixed device. The next time the compressor started the high pressure and low pressure would be the same and the compressor would start with no assistance. As system efficiency increased more systems have been equipped with a self regulating metering device called a Thermostatic Expansion Valve or TXV. This device is a self adjusting metering device that will close off when the system shuts off. High pressure and low pressure will take much longer to equalize with this type of metering device so their is a good chance the compressor will cycle back on with a differential between the high pressure and low pressure. This causes a need for increased torque to start the compressor motor. This additional torque is generated by adding some type of starting components to the system.
Common start assist devices are a start capacitor with start relay, start capacitor with some type of thermal shut off and start thermistors. The start capacitor and start relay as well as the thermistor style must be matched to the application. The style with the thermal shut off are generic replacements that are typically used as a quick fix.
There are 2 different types of capacitors used in the HVAC field. The types are start capacitor and run capacitor.
A start capacitor is called a start capacitor because it is in operation only when the motor is starting. This design increases the torque of the motor allowing a compressor to start against a load. This design is not used with a fan motor. It is used in conjunction with some type of relay that removes it from the circuit as a motor approaches full speed. This type of capacitor is encased in a bakelite case and is air cooled. It is not filled with oil and it is usually a round design.
The most common type of capacitor is a run capacitor. It is designated as a run capacitor because it stays in the circuit while the motor is operating. The purpose of a run capacitor is to increase motor starting torque as well as increasing the efficiency of the motor during operation. This capacitor is in a plastic or metal can and is filled with oil. The purpose of the oil is to help cool the internal plates during operation. This capacitor can be either round or oval shape.
The best way to identify the correct capacitor is using the correct nomenclature from the HVAC equipment nameplate. Getting the correct factory part will keep your UL listing intact and you will know your equipment is operating at factory specs. Sometimes the tag is not legible on older units. I have added an image showing the tag on 2 different brands of capacitors. The information required for replacement is the uf rating and the VAC rating. As you can see there are 2 different ways to list the information used by 2 different manufacturers. In the image the capacitor on the left lists the uf ratings as 50/5 uf and 440 VAC. The capacitor on the right lists the same ratings as 50 uf 5 uf and 440VAC.
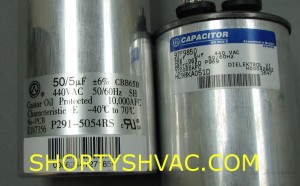
The capacitors we show in the picture are manufactured for Carrier Corporation with a Carrier part number on each one. The capacitor on the right has Carrier part number HC98KA051D. The D in this part number is not used so the actual part number is HC98KA051. This part number has been replaced by Carrier with a new part number. New part number P291-5054RS is the factory replacement for HC98KA051. If you provide the product number from the Carrier equipment you are servicing we have access to a Carrier database that lists the current Carrier part number for all parts used in your equipment. By providing the product number you can be assured you will get a brand new Carrier factory part and your equipment will be operating at its original specs and efficiency.
Run capacitors used in HVAC applications can be either round or oval shape. They also can be either a single or dual capacitor. A single capacitor has one set of plates and is used for the operation of one motor. A dual capacitor is actually two capacitors in one shell sharing a common plate. Dual capacitors are used for the operation of two motors. The two different type of capacitors can be differentiated by the terminals on top. A single capacitor will have two terminals and a dual capacitor will have three terminals on top. The two internal capacitors share a common plate for both motors labeled C on the top of the capacitor. The other terminals will be labeled FAN for the fan motor and HERM for the compressor. It is very important to make sure the wires go back on the same terminals when replacing a capacitor. A capacitor can fail and cause the fan motor and compressor not to start. The top of the capacitor should be perfectly flat. If it is slightly domed or has any type of oil leak it should be changed. Bad bearings in a fan motor can cause a capacitor to fail. Capacitor failures are very common during heat waves as excess heat does cause damage. Make sure power has been disconnected before making any repairs. In the picture below the capacitor on the right is slightly domed. Notice the flat top on the new capacitor on the left. Also notice the terminals are clearly marked.
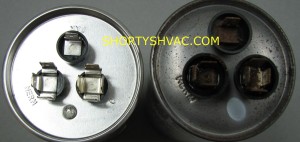
Helping with Do It Yourself Funace and Air Conditioner Repairs